Founded in 1949 by Phil’s grandfather, Phil is Head Grower at APS Group (A Pearson and Sons), a family-owned fourth generation horticulture business.
The business grew from a single nursery in Cheshire and today, APS Group are the UK's largest tomato supplier and produce packer, supplying 40% of the UK tomato market, with glasshouse nurseries in Cheshire, Kent, the Isle of Wight, Elloughton, Drax, and Teeside.
The operation covers a total area of 70 hectares of glasshouses, two packing sites and employs 1800 people.
Driving innovation
APS Group grow over 160 different varieties of tomato, anything from picolino to beef steak tomatoes and everything in between. They also grow other fresh produce such as 20 different types of pepper and six different types of aubergine.
Phil is driven to improve the sustainability of British fresh produce production and has been the driving force for innovation in the business, which has led to the development of new technologies.
Growing conditions
The glasshouses produce around 650 million tomatoes per year. Technology plays a major part in creating the perfect growing conditions in the most energy efficient way. APS Group uses controlled environmental conditions in the form of vertical farming, hydroponics and LED lighting to increase energy efficiency and ensure the best quality produce.
The LED lighting not only provides season extension, but uses less electricity than traditional sodium lighting. Only the wavelengths needed for absorption by the plants are used. This allows for maximum energy efficiency and optimal growing conditions all year round.
Computer systems automatically close the screens of the glasshouses just before night, locking in the sun’s warmth. Furthermore, herbicides are not used, and the use of pesticides is almost non-existent, because the controlled environment allows management of weed, pest and disease pressures.
No weeds are present, and the hydroponics, IPM (Integrated Pest Management) which has been used in glasshouses since the 1960s, and any fungal diseases are controlled by keeping the environment dry though the use of warm water supplied to heating pipes at 35-40°C.
In addition, the water is enriched with fertiliser, and excess irrigation solution is recycled, meaning there are no nutrient losses to the environment and cost savings are made by nutrient management being so efficient.
Combined Heat and Power
APS Group have been pioneering in driving forward agri-tech and sustainability. They use CHP (Combined Heat and Power) engines to generate electricity to sell to the local grid, supplying over 211,500 megawatt hours of electricity annually to the National Grid which powers over 200,000 homes.
Figure 1. The glasshouses on the Isle of Wight
CHP is innovative because it makes use of the by-product of electricity generation. The waste heat is used to warm the greenhouses and the waste carbon dioxide is delivered to the tomato plants to increase the rate of photosynthesis.
The use of CHP is innovative because it is more efficient by avoiding losses and reducing emissions. CHP has been so effective that APS Group provide 60% of the electricity generated for the Isle of Wight. Furthermore, the produce quality is improved because the carbon dioxide increases yield, creates a thicker cell wall and increases the sugar level, and therefore fruit flavour.
Converting leaf waste
The nursery in Cheshire has developed a unique AD (Anerobic Digestion) plant that uses all the tomato crop’s leaf waste and converts in into valuable by-products that can be used in the growing operation.
Around 20 years ago, the AD plant was first implemented to generate energy in the form of biogas. However, there was not much energy produced from the tomato leaves, so instead of producing energy, the by-products from the AD were used in a different way. The liquid digestate can be used as a fertiliser, however, the system synthesizes the leaf cellulose to produce compostable packaging. The ‘pulp’ is dried to make punnets which are compostable in 11 weeks.
The company also works with a packing business in the Lake District to produce a unique type of cellophane, which can be used with automated packing machines. Packing is important for keeping food fresher for longer and the ‘bio-based’ punnets also have an impact on the respiration of the fruit, increasing shelf-life.
Overall, the AD plant turns 3.5 tonnes of leaf waste into a range of products, including environmentally friendly packaging every year. This is an elegant and innovative solution to a waste management problem.
Environmental and productivity benefits
Phil believes that working with nature is the best way to produce the tastiest, healthiest crops.
APS Group have created a business which is low input, efficient and utilises technology in the form of computer models, CHP and AD to be more economically and environmentally sustainable.
Furthermore, producing crops in the UK reduces reliance on food imports, which is better for food security and the environment because less food miles are involved.
Read more on tackling food waste:
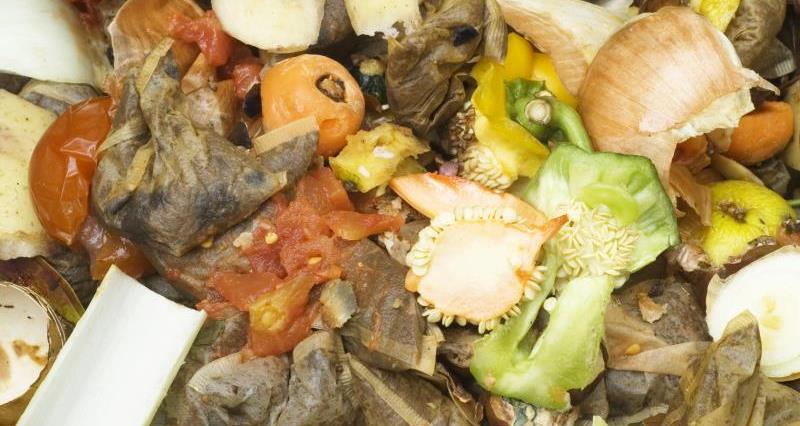